At a Glance
The Performance Validation Team successfully conducted a thorough commissioning project at Bates Technical College for the Center for Allied Health Education, formerly the Medical Mile Health Science Center. This cutting-edge, three-story educational facility spans 65,000 square feet including a dedicated parking level. The facility serves as an advanced addition to the college campus, located in downtown Tacoma, Washington.
Designed to deliver state-of-the-art vocational training, the center includes advanced classrooms, specialized training spaces, and faculty offices. It serves as a hub for a wide variety of health education programs including dental laboratory technology, denturist, hearing aid specialist, medical assistant, practical nursing, nursing assistant, occupational therapy assistant, planned technician, acute care nursing assistant, and medical technology. The center also features a comprehensive set of general science labs, cadaver labs, and a versatile SIMLAB for hands-on training across all programs. The center drives a significant step forward for the institution to deliver exceptional health education.
LEED Silver Certification – Compliance for Optimized Energy Efficiency
The commissioning of the Medical Mile Science Center was driven by the overarching goal of obtaining LEEDv4 Silver certification. Our team of commissioning engineers supported this objective by conducting LEED fundamental and enhanced commissioning to ensure all systems operated in compliance with certification standards while reducing environmental impact.
Our team met the stringent requirements for LEED Energy and Atmosphere Option 1, Path 2, Enhanced and Monitoring-Based Commissioning, Fundamental Commissioning, and Envelope Commissioning. Executed through a comprehensive approach of system verification, back checks, and communication with primary project stakeholders to ensure all commissioning-specific points for certification were effectively achieved.
The systems of commissioning for compliance included the domestic hot water, plumbing pumps, HVAC, DDC controls, lighting control, power service and distribution, and utility metering.
Our proactive, collaborative, and diligent project approach was instrumental in ensuring compliance with LEEDv4 Silver certification, while also upholding our commitment to delivering outstanding sustainable building practices.
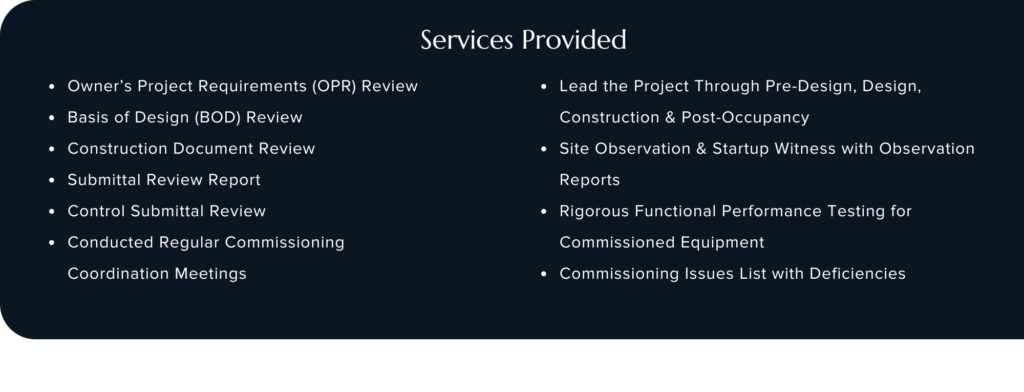
Optimizing Building Systems
The commissioning of the three-story 65,000 square foot facility spanned the domestic hot water, plumbing pumps, HVAC, DDC controls, lighting control, power service and distribution, and utility metering. With the goal of driving optimal installation, system operation, and energy efficiency to comply with the LEED Energy and Atmosphere Option 1, Path 2, Enhanced and Monitoring-Based Commissioning, Fundamental Commissioning, and Envelope Commissioning for obtainment of certification points.
The team adopted a comprehensive approach to testing, verification, back-checking, and evaluation to ensure every aspect of the building’s systems performed optimally. During the testing phase, the team added significant value by identifying several issues: an unoccupied air handler, non-calibrated VAV units, dampers and chilled water valves working backward, and electric heaters that were over- and under-heating. Identifying these issues during the testing phase not only optimizes functionality but also saves significant energy consumption in the long term.
Additionally, the team employed a meticulous approach to project documentation and reporting. This began with the development of the Owner’s Project Requirements (OPR) document, followed by a review of the Basis of Design (BOD) and the design review. During the design review, the team identified several incorrectly sized airflow diffusers and suggested fixes for sizing reconciliation. Furthermore, they recognized the need for more detailed installation drawings for the systems, which facilitated proper installation from the outset.
Ensuring that all objectives are met is critical to our process. This is achieved through the development of test forms, the conduction of tests, and the reporting and identification of issues with the appropriate stakeholders. These steps ensure an effective, communicative, and efficient project delivery.
Strategic Flexibility: Navigating Challenges with Solutions and Adaptability
During the commissioning of the facility, our team of engineers navigated numerous challenges with a steadfast commitment to delivering system excellence through persistence communication. Each challenge was addressed with a tailored approach to ensure that every system was verified, tested, and backchecked prior to final resolution.
One obstacle encountered involved the facility lighting, specifically difficulties in fine-tuning due to malfunctioning sensors. While installation was confirmed to have been conducted correctly, the sensors themselves were found to be faulty. Consequently, replacement of sensors was required across multiple rooms within the facility.
During the verification of building systems, it was observed that the building experienced excessive pressurization, resulting in difficulty opening or closing doors within the facility. Given the facility’s primary function as a lab space, a significant amount of air was being extracted when unoccupied. This experience provided a valuable learning opportunity for our team, as the issue resolved itself upon occupancy.
Furthermore, it was observed that the CO2 sensors for several rooms registered levels well above 200 ppm, which is highly unlikely. Consequently, all sensors throughout the facility underwent recalibration. Subsequently, it was determined that the entire batch of sensors was faulty, necessitating their replacement. Identifying this issue was vital for the long-term well-being of the occupants, as failure to do so could have resulted in significant issues later on.
Ultimately, our team employed consistent communication, persistence, and diligence to ensure that all identified issues were resolved effectively and efficiently. This ensured that facility teams were well-prepared for success upon building occupancy and that systems were operating optimally upon project delivery.
Ensuring Long-Term Excellence: Post-Project Support and Warranty Period Commitment
The Performance Validation Team is committed to ensuring long-term excellence for every building we support. This commitment begins in the post-occupancy phase, after the building has been turned over. Our team is dedicated to conducting meticulous and thorough checks to ensure optimal system performance and seamless transition to the facility maintenance team.
During the post-occupancy review of the facility, several primary issues needed resolution prior to project completion. Five different spaces in the facility had temperature readings in Celsius instead of Fahrenheit, an issue linked to the electrical panel. The trends were not set up due to a problem integrating the panel with the main server. Once integrated, the team verified the correct display. Additionally, the stairwell lighting was too dim upon final installation, despite being installed according to the design. This prompted the team to recommend increased lighting levels to enhance safety for facility occupants. Furthermore, the team discovered that a chilled water heater had been running continuously for an entire month, significantly impacting the facility’s energy usage. This finding provided an opportunity to back-check the settings of the chilled water systems to prevent similar occurrences in the future.
A key component of our post-occupancy process is ensuring that maintenance teams have the necessary information to effectively manage, optimize, and adjust systems for years following project completion. To support this, the team developed a monitoring-based plan for fault detection, enabling maintenance teams to easily reverify the building every few years without having to reference the OPR, thus ensuring the building operates as designed. The Performance Validation Team is committed to equipping building owners with the necessary tools and knowledge to ensure efficient operations for years to come.
Project Summary
The Performance Validation Team played a crucial role in successfully delivering the Medical Mile Health Science Center at Bates Technical College. As a third-party commissioning provider, the team was dedicated to achieving operational excellence through optimized systems. The project involved comprehensive enhanced and fundamental commissioning scope for the new three-story, 65,000-square-foot educational facility. Serving as a hub for medical education, the center is dedicated to providing quality vocational training for students.
As the commissioning authority, our primary objective for the project was to secure the necessary commissioning points for LEEDv4 Silver certification by ensuring optimized, energy-efficient systems throughout the facility. This involved detailed testing, back-checking, and verification of systems, including domestic hot water, plumbing pumps, HVAC, DDC controls, lighting control, power service and distribution, and utility metering. Our comprehensive approach facilitated the effective execution of LEED Energy and Atmosphere Option 1, Path 2, Enhanced and Monitoring-Based Commissioning, Fundamental Commissioning, and Envelope Commissioning.
Through diligent collaboration, consistent communication, and preemptive project management, our team successfully delivered the comprehensive building and system commissioning required to achieve LEEDv4 Silver certification. Our team of engineers is dedicated to providing clients with facilities that perform optimally for years beyond the warranty period.