At A Glance
Our team conducted a comprehensive 1-day smoke study for a pharmaceutical client based in Illinois. Although this study was not mandated by the Food and Drug Administration (FDA), it held immense significance for our client. The primary objective was to verify the safety of their employees throughout the production process of a specific product, focusing on any potential leaks from the production area. By conducting this non-FDA-regulated study, we aimed to provide assurance that there were no chemical leaks occurring during the client’s standard operations.
ALIGNMENT WITH THE CLIENT DELIVERED EXPECTED RESULTS
As this smoke study was not FDA mandated, it was crucial for us to listen closely to the client’s needs in order to perform the study according to their specific expectations. To achieve this, we organized an on-site meeting to thoroughly understand their requirements.
During the meeting, we diligently listened to the client’s concerns, goals, and expectations. This was essential as it allowed us to develop a tailored plan that aligned precisely with their needs. By incorporating their input, we ensured that the study would be conducted in a manner that met their expectations.
Since there were no regulatory guidelines to follow, it was crucial for our team to rely on the client’s insights to define the scope and objectives of the study. By actively listening to their requirements, we were able to create a study plan that addressed their concerns regarding product contamination within the production area.
This client-centric approach was crucial for delivering results, providing assurance regarding employee safety, and creating confidence production processes.
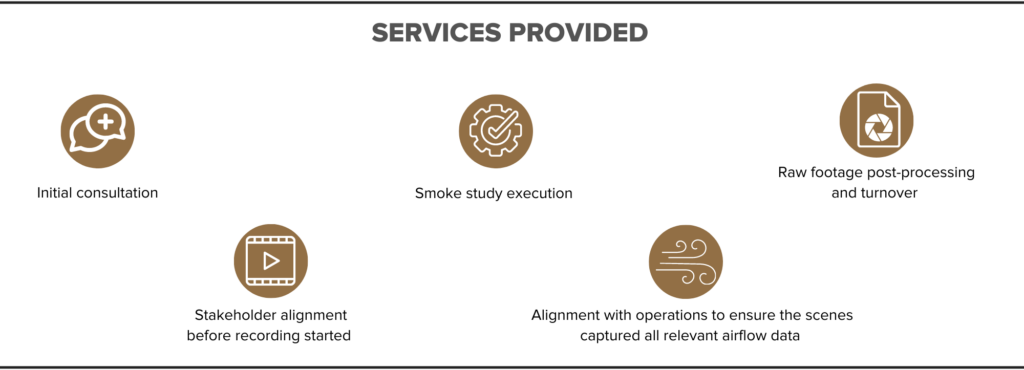
Our team’s experience with multiple foggers and cameras was crucial to the project’s success.
Due to the timeframe and size of the room, this project required the use of four cameras and two foggers. Also, to ensure optimal visibility on camera, black backdrops were utilized. The planning phase required careful consideration to determine the precise placement of the cameras, ensuring accurate capture of the airflow dynamics within the room.
The primary objective of the study was to analyze and document the behavior of the airflow when the doors were opened and left open. This involved capturing detailed footage of the area, specifically focusing on how the smoke dispersed and moved in response to the changing airflow patterns.
The implementation of the study involved strategically positioning the cameras to cover the entire room, allowing for comprehensive visual documentation. The foggers were used to visualize the environment, generating smoke that mimicked potential airborne particles. By meticulously coordinating the timing and execution, we were able to capture precise details of the airflow within the room during different door states.
Throughout the project, significant emphasis was placed on planning and execution to ensure accurate and reliable results. The use of black backdrops enhanced visibility, enabling a clear view of the smoke movement, and facilitating detailed analysis. By effectively utilizing the cameras and foggers, we obtained comprehensive footage that provided valuable insights into the airflow dynamics when the doors were opened and left open.
WE DELIVERED OPERATIONAL CONFIDENCE IN THEIR SAFETY MEASURES
Ultimately, the objective of this smoke study was to evaluate the airflow within the production area, particularly in relation to the material transfer and personnel doors. These doors were equipped with a safety alarm that triggered if they remained open for a duration exceeding 10 minutes. A key aspect of the study was to examine whether the air did not escape within this 10-minute timeframe and to determine if this time limit was appropriate.
The results of the study provided conclusive evidence that the 10-minute alarm setting was indeed acceptable. This finding is crucial as it equips the client’s safety team with empirical data supporting the established time limit for the sliding doors. By demonstrating that the air movement remained within the desired parameters, the study affirms the effectiveness of the containment and provides reassurance about the overall safety of the production area.
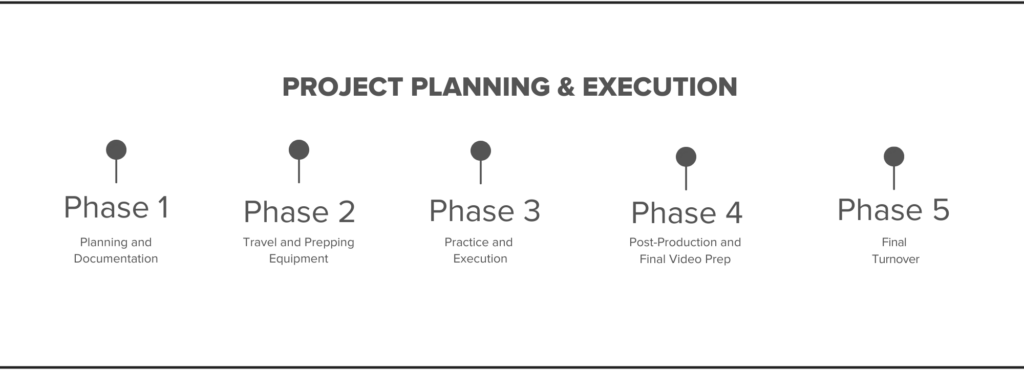
WE ALSO PROVIDED AD-HOC CHECKS FOR STAKEHOLDERS
Near the end of the day, our team performed a number of ad-hoc checks for different stakeholders that wanted to see how the air flowed in specific areas of the production room. This involved opening and closing doors, holding the fogger at different locations, and emulating production steps to ensure the client saw everything they needed to.
These tests were outside of our initial plan, but we were happy to perform them to help the client understand how air moved in their production area.
Project Summary
Our comprehensive 1-day smoke study for the pharmaceutical client in Illinois not only verified the safety of their employees during production but also demonstrated our commitment to aligning with their specific needs. By incorporating their input and utilizing four cameras and two foggers with black backdrops, we captured precise details of the airflow dynamics within the room. The study provided crucial evidence supporting the effectiveness of the 10-minute alarm setting for the sliding doors, reinforcing the efficacy of the Restricted Access Barrier (RAB). Our flexibility in performing ad-hoc checks showcased our dedication to meeting stakeholder requirements and ensuring a thorough understanding of the airflow patterns in the production area. This project has delivered operational confidence and instilled trust in the client’s safety measures, highlighting our expertise and commitment to client satisfaction.