At A Glance
The project focused on launching a new advanced medical drilling system aimed at enhancing surgical precision and effectiveness. Spearheaded by a leading medical device manufacturer, the project included a rigorous Production Part Approval Process (PPAP) to ensure all components adhered to the highest quality and safety standards. This project represented a significant escalation in scope for the Performance Validation team, involving comprehensive management and validation of numerous components, markedly more extensive than any previous efforts. The scale and complexity of this multi-year project not only highlighted its ambitious nature but also set a new industry standard for manufacturing excellence and reliability in medical technology.
Mastering the Art of Precision and Validation Complexity
This project represented an enormous undertaking by the Performance Validation team, tasked with the complex challenge of overseeing the PPAP for an entirely new line of medical drilling equipment. The project’s scope was expansive, involving detailed scrutiny and validation of many components critical to the equipment’s functionality and safety.
Each component was part of a comprehensive top-level PPAP, with its own set of documents, ensuring compliance with the stringent quality standards set forth by the medical device manufacturer. The process was not just about adhering to specifications but also about ensuring that each part would consistently perform under the stresses of real-world surgical applications. This required a meticulous approach to validation, testing, and documentation, which was significantly more intensive than any prior projects handled by the team.
Moreover, the project’s complexity was elevated by the need to coordinate among multiple suppliers, each contributing various parts from different global locations. Managing these relationships and ensuring a seamless integration of parts into the final product required a high degree of coordination and technical expertise.
The efforts spanned several years, illustrating not only the project’s vast scale but also its critical importance to the future of surgical practices. This extensive timeline was necessary to accommodate the iterative process of testing, feedback, and revisions, which ensured that every component could reliably meet the operational demands expected of innovative medical equipment.
Through this project, the team set new benchmarks for precision, reliability, and quality in medical device manufacturing, paving the way for future innovations in the field.
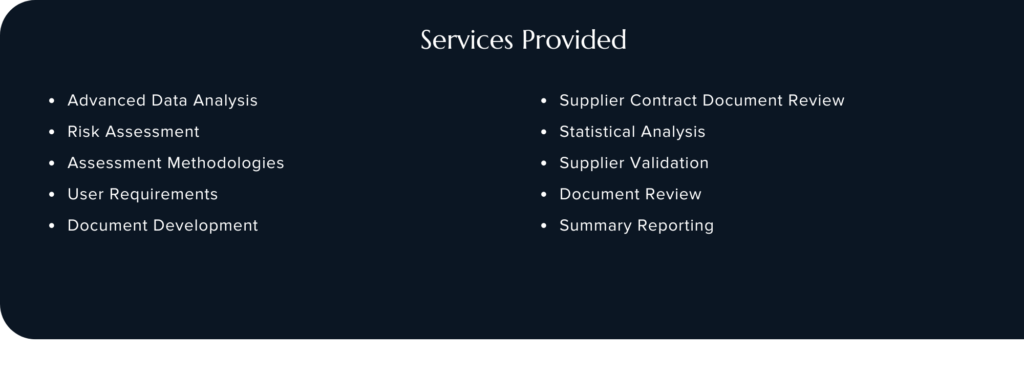
Navigating Complex Challenges
The project encountered several significant challenges that tested the resilience and adaptability of the Performance Validation team. These obstacles were multifaceted, spanning logistical, technical, and communication domains, each adding layers of complexity to the project’s execution.
Technical Challenges: From a technical standpoint, the greatest challenge was ensuring that each component met the stringent design specifications and documentation requirements under the comprehensive PPAP. The Performance Validation team focused on detailed technical assessments to verify that all components adhered to the quality standards set forth by the medical device manufacturer. This involved meticulous documentation and quality assurance processes to ensure each part complied with the precise demands of medical applications, often requiring several iterations to resolve issues related to component specifications and compliance.
Communication Barriers: Effective communication was critical given the project’s scale and the diversity of stakeholders involved. However, the team faced significant barriers, including language differences and time zone discrepancies, which complicated clear and timely interactions. Ensuring that all parties—ranging from local teams to international suppliers—were aligned on project goals and updates required diligent communication protocols and frequent virtual meetings. These challenges demanded a high level of expertise, patience, and collaborative effort to overcome, highlighting the team’s commitment to maintaining project integrity and timelines. By addressing each hurdle strategically, the project not only progressed despite these obstacles but also provided valuable learning experiences that enriched the team’s problem-solving capabilities.
Benchmarking Success: Enhancing Efficiency, Reducing Risk, and Improving Reliability
The successful completion of the PPAP marked a significant achievement for the Performance Validation team, demonstrating their ability to exceed the medical device industry’s stringent requirements. The rigorous application of the PPAP process led to high-quality outcomes that met and often surpassed industry standards, enhancing the drilling system’s reliability and effectiveness in surgical settings. The project’s benefits included improved production efficiency, reduced risks, and enhanced reliability of the medical devices produced, setting new industry benchmarks, and providing a robust model for future projects.
- Improved Efficiency: Streamlining the PPAP process led to more efficient production cycles. The lessons learned and the methodologies developed during this project have been instrumental in reducing time-to-market for new products, thereby enhancing the manufacturer’s ability to respond to market needs swiftly.
- Reduced Risks: By PPAPing each component, the team was able to identify and mitigate potential risks early in the development cycle. This proactive approach to risk management not only safeguarded the project against delays and cost overruns but also ensured that the final product met all safety and performance criteria without fail.
- Enhanced Reliability: The exhaustive testing and validation process contributed to an exceptionally high reliability rate for the medical drilling systems produced. This reliability is critical in medical settings, where product failure can have serious implications. The enhanced reliability has not only bolstered the manufacturer’s reputation in the market but also contributed to greater trust and satisfaction among end-users.
Blueprint for Success: Strategic Lessons and Best Practices from Medical Device Validation
The project not only achieved its objectives but also provided invaluable insights and established robust practices that will guide future initiatives. The lessons learned and best practices identified are fundamental to the ongoing improvement of project management and execution strategies within the medical device manufacturing industry.
Lessons Learned:
- Early Supplier Engagement: One of the key lessons learned was the critical importance of engaging suppliers early in the project lifecycle. This early engagement facilitated better alignment on project requirements and quality standards, ensuring that suppliers were well-prepared and proactive in meeting the complex demands of the project.
- Clear Communication Channels: The project underscored the need for establishing clear and effective communication channels among all stakeholders. Regular updates, clear protocols for information exchange, and well-defined points of contact helped mitigate misunderstandings and kept the project on track despite the geographical and cultural diversity of the teams involved.
- Feedback Integration: Incorporating continuous feedback loops throughout the PPAP process proved invaluable. These loops allowed for real-time adjustments and improvements, ensuring that any issues were addressed promptly and efficiently, thereby reducing delays, and enhancing the quality of the final product.
Best Practices:
- Early Integration of Design and Production Teams: Ensuring that the design and production teams were integrated from the outset was crucial. This collaboration enabled a comprehensive understanding of the technical requirements and facilitated a design-for-manufacturability approach, which streamlined the production process and minimized costly redesigns.
- Robust Project Documentation: Maintaining detailed and accurate documentation throughout the project was another best practice that contributed significantly to its success. This documentation served as a vital tool for quality assurance, regulatory compliance, and as a reference point for resolving potential issues. It also facilitated a transparent audit trail that could be used to demonstrate compliance and inform future projects.
Project Summary
This case study details the successful implementation of the Production Part Approval Process (PPAP) by a leading medical device manufacturer for launching a new advanced medical drilling system, aimed at enhancing surgical precision and effectiveness. Despite facing significant logistical, technical, and communication challenges, the Performance Validation team adeptly managed multiple global suppliers and ensured seamless integration of parts. The successful completion of the PPAP not only set new industry benchmarks for production efficiency, risk reduction, and reliability but also established robust best practices that will guide future projects, highlighting the manufacturer’s commitment to innovation and excellence in medical technology.