At a glance
In a landmark project within North Carolina’s Research Triangle Park, Performance Validation (PV) executed a comprehensive temperature mapping study for a leading pharmaceutical manufacturer’s state-of-the-art Automated Storage Retrieval System (ASRS) facility. Spanning two crucial storage areas—Controlled Cold Temperature (CCT) with >9000 pallet positions and Control Room Temperature (CRT) with >8000 pallet positions—the project utilized 371 Vaisala Data Loggers to ensure precise temperature control critical for drug product storage. The initiative encompassed extensive mapping under various conditions, including empty, simulated full, and open door scenarios, to validate compliance with the United States Pharmacopeia (USP). Leveraging advanced data analysis and risk assessment methodologies, the project addressed unique ASRS challenges, ensuring optimal operational efficiency and product and patient safety through innovative temperature management solutions.
Navigating Complexity: Mastering Data Logger Placement in High-Density Storage
The project’s initial hurdle was the precision required in positioning data loggers within the high-density, automated storage configuration. This task necessitated an in-depth understanding of the ASRS architecture and meticulous planning to ensure comprehensive temperature monitoring coverage.
Performance Validation tackled this challenge head-on by conducting a detailed analysis of the facility’s blueprints and leveraging industry best practices. This enabled the strategic deployment of 371 data loggers, ensuring every critical area within both the CCT and CRT spaces was accurately monitored, thus guaranteeing the integrity of the temperature mapping data.
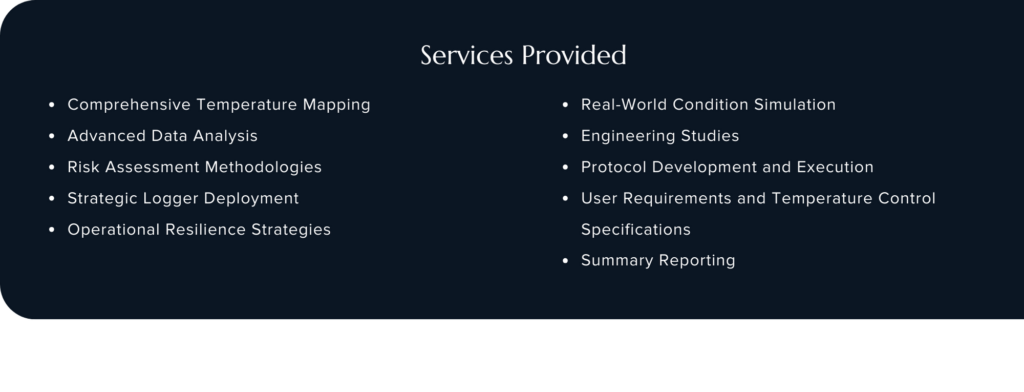
Overcoming Adversity: Responding to Unforeseen Operational Challenges
Unexpected operational issues, including equipment failures and power outages, threatened the integrity of the temperature mapping process. These variables introduced significant complexity, requiring flexible and adaptive strategies to maintain project continuity and data accuracy.
The team’s response was twofold. Firstly, they swiftly adapted to these challenges by modifying the test protocol to accommodate for the interruptions, ensuring data collected reflected normal operational conditions. Secondly, the occurrence of equipment failure prompted an in-depth engineering study, reassessing the operational requirements of equipment systems to meet storage space condition requirements leading to strategic operational modifications.
Enhancing Operational Resilience: Simulating Real-World Conditions
Accurately predicting the temperature dynamics within a fully stocked dense-storage warehouse posed a unique challenge, necessitating the simulation of real-world conditions to validate the ASRS’s operational resilience.
Performance Validation strategically placed pallets to restrict air flow throughout the space alongside load pallets equipped with loggers, creating a simulated worst-case full-stock scenario. This approach provided invaluable insights into the system’s performance under various operational conditions.
Additionally, Performance Validation provided testing within different operational worst-case conditions, including door openings, thereby ensuring the facility’s readiness for real-world demands.
Engineering Insights: Beyond Temperature Mapping
During the temperature mapping process, it emerged that the existing fans might not be essential for maintaining the temperatures within regulatory standards—prompted a closer examination. Performance Validation undertook a targeted engineering study to explore the ramifications of shutting off these fans. The results confidently affirmed that deactivating the fans wouldn’t compromise the safety and integrity of the stored products. This crucial insight led to a shift in the client’s local equipment management strategy, specifically influencing changes in their latest facility based on findings from RTP. They not only switched to a different type of fan but also implemented new servicing protocols. This adaptation highlights the study’s value, showing its impact extended beyond the initial temperature control concerns, leading to enhanced operational efficiencies and cost savings through reduced maintenance, minimized downtime, and lower energy consumption.
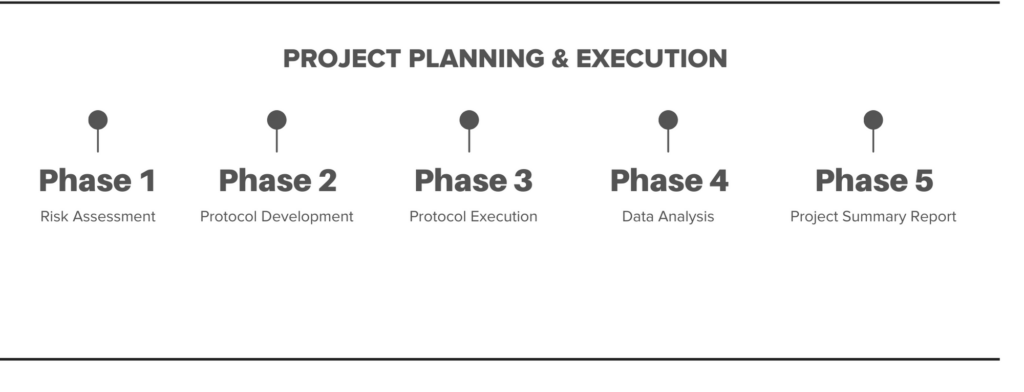
Achieving Operational Excellence: The End-to-End Benefit of Precision Temperature Mapping
Operational Excellence in the Face of Challenges: The project’s success in adapting to unforeseen operational hurdles, such as power outages and equipment failures, demonstrated Performance Validation’s capability to maintain project integrity under adverse conditions. The swift adjustments made to testing protocols and the subsequent engineering study that led to the strategic fan shutdown underscored a proactive approach to operational resilience. This adaptability ensured uninterrupted compliance and operational efficiency, minimizing risk to product integrity.
Simulated Scenarios Informing Real-World Preparedness: By simulating full-stock conditions, Performance Validation not only validated the ASRS’s temperature management under theoretical conditions but also provided actionable insights for real-world application. This forward-thinking strategy enhanced the facility’s operational readiness, ensuring that the temperature-controlled environment would reliably support the manufacturer’s logistical and storage needs under varying conditions, protecting product and patient safety.
Summary: Setting New Standards in Temperature-Controlled Storage
Performance Validation’s temperature mapping project in Research Triangle Park exemplifies innovative solutions in ensuring regulatory compliance and product safety for automated storage systems within the biopharmaceutical industry. By skillfully navigating complex storage configurations, responding with agility to operational challenges, and delivering strategic insights that extend beyond immediate project goals, this initiative not only met pharmacopeia standards but also advanced operational efficiency and sustainability for the client. The project stands as a benchmark in the industry, showcasing the importance of precision, adaptability, and innovative problem-solving in maintaining the integrity of temperature-sensitive pharmaceutical products.