Overview
A global pharmaceutical manufacturer was looking to boost its production capacity due to high market demand but was running out of space at its largest U.S. facility. The manufacturer’s team decided to recapitalize its existing warehouse space to make room for a new device line. After a rigorous qualification process, the manufacturer procured a Dematic Automated Storage and Retrieval System (ASRS) to leverage vertical product storage and reclaim valuable square footage to accomplish this goal. After the ASRS installation, Performance Validation (PV) worked with the manufacturer’s automation team and Dematic’s onsite team to validate the entire ASRS process while identifying gaps and implementing solutions to limit costly service interruptions. The automated warehouse would serve up to 20 different lines, so minimizing downtime would be critical to the project’s success.
Problem
- The manufacturer was running out of space and wanted to install new lines for increased capacity.
- The manufacturer had limited experience working with Dematic and Dematic’s systems/controls.
- Staying on schedule for the ASRS launch and minimizing any downtime after go-live would be critical in maintaining production output for all device assembly and packaging lines at the facility.
The Solution
The pharmaceutical manufacturer’s onsite automation engineering team initially approached PV for its expertise in automated equipment validation and computer software validation (CSV) and previous experience with automated warehouse solutions. Within an extremely tight three-month execution timeframe (see the engineering shakedown and validation phases in the graphic below), PV worked with the manufacturer to develop a process for identifying — and solving — potential disruptions in the ASRS that could lead to expensive downtime and possible setbacks. PV’s collaboration with the manufacturer on a rigorous Engineering Shakedown was the critical success factor in the project’s overall success. The 10-week shakedown process identified unique scenarios that could have resulted in potential issues. Working together as a team with both Dematic and the manufacturer’s automation engineers, PV was able to manage to correct these issues before Validation even began. PV started by addressing overall system safety activities before moving to manual equipment controls. Once the core components were functioning seamlessly, PV began evaluating the inbound and outbound pallet transfers and then evaluating fully automated controls. Ultimately, the Engineering Shakedown allowed PV to explore hundreds of potential disruption scenarios so that the final validation saw little-to-no surprises and was completed in only two weeks.
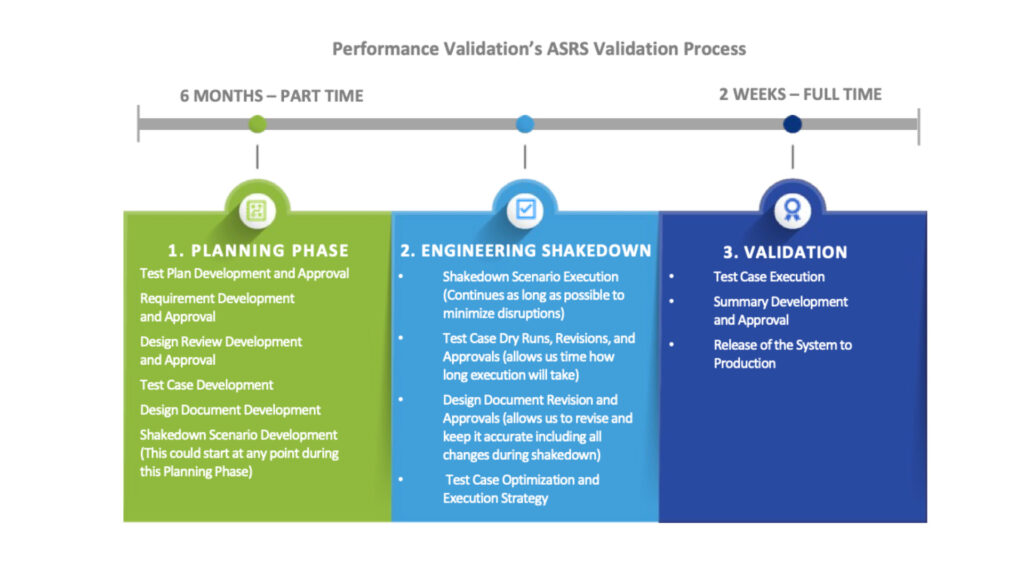
The Results
The manufacturer was thrilled with the project results. The PV and manufacturer’s automation team helped deliver a validated Automated Storage and Retrieval System (ASRS) that exceeded expectations around ASRS efficiency. The new Dematic Automated Storage and Retrieval System (ASRS) downtime is less than two hours a week on average, while other similar sites (using different ASRS systems) have reported downtimes exceeding 20 hours per week. Furthermore, by backing out the testing schedule during engineering shakedown, PV ensured that the warehouse would be fully operational by the required timeline.
Benefits of Working with Performance Validation
- PV is an expert in the commissioning, qualification, and validation of complex capital equipment, which helps Pharmaceutical manufacturers meet aggressive schedules, hit ROI targets, and achieve and maintain compliance.
- PV is committed to being part of the solution, working side by side with vendors, customers, and internal team members to find real-world solutions at the ground level.
- PV is relentless in its pursuit of excellence. During the entire validation process, PV was focused on the system maintaining product identity, and no products were damaged.
- PV “takes on the client’s pain as its own” with the ability to provide seasoned staff and resources around the clock to ensure a job is done well and on time.
- PV validation engineers are lifelong learners who love what they do. They are driven to seek continual improvements, bringing a passion for problem-solving and extensive experience to every job.
Have a question about the ASRS validation process? If so, please get in touch with us through our Contact Us Form (https://perfval.com/contact-us/) and one of Performance Validation’s team members will be in touch.
About Performance Validation: Performance Validation is a 100% employee-owned company that has been serving the life science industries since 1988 and is a nationwide leader in providing commissioning, qualification, and validation (CQV), and building commissioning (Cx) services to FDA regulated pharmaceutical, medical device manufacturing, drug distribution facilities, to federal, state, and local government facilities and commercial building owners.
For more information:
David Tebbe
Principal Validation Engineer