At A Glance
Performance Validation (PV) was enlisted by a renowned Michigan-based medical device manufacturer to facilitate a complex and strategic relocation of eight production lines. This project involved transferring the manufacturing of ear, nose, and throat (ENT) single-use, sterile devices to a newly established facility in Kalamazoo.
The primary goal was not just the physical relocation of production lines, but also the establishment of these lines in an environmentally controlled area. A significant focus was placed on setting up a newly qualified cleanroom and utility service adhering to stringent quality and regulatory standards.
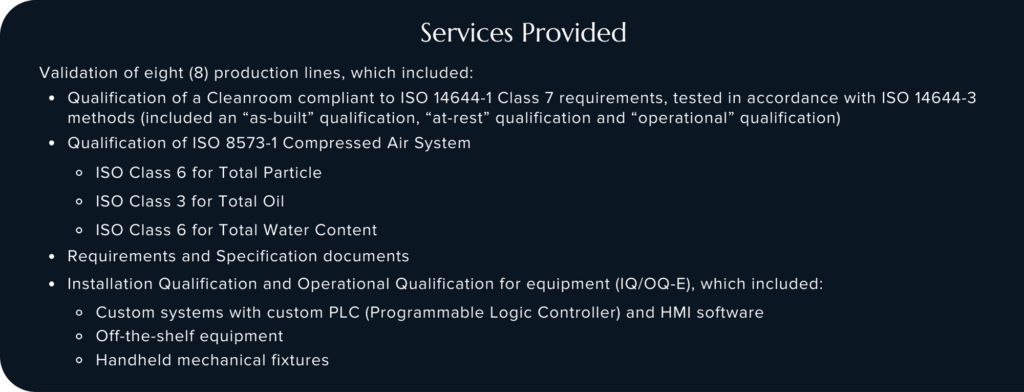
Leveraging Prior Experience in Coordinated Quality Systems for Dual-Site Line Transfer
This project presented a unique challenge: transferring production lines across two distinct locations. Recognizing the complexity of such an endeavor, our client sought a partner with a proven track record in managing large-scale transfers. Performance Validation (PV) was the chosen collaborator, bringing valuable experience from successfully executing two similar line transfers for this client.
The project strategy involved the deployment of two specialized teams. The client’s team, composed of engineers and Subject Matter Experts (SME) was stationed at the original manufacturing site, while the PV team was positioned at the receiving facility in Kalamazoo. This dual-site approach was crucial for a seamless transition.
The initial phase focused on Building, Facility, and Utility Qualification at the new site, adhering to the rigorous ISO 14644-1 Class 7 standards. This was a vital step in ensuring the new cleanroom facilities not only matched but exceeded the standards of the original site. The cleanroom underwent a thorough qualification process, evaluated in its ‘As Is’, ‘At Rest’, and ‘Operational’ states to ensure full compliance and operational integrity.
A meticulous and strategic approach was adopted for the line transfer. Commencing with Line One, each production line was methodically validated and relocated. Post-integration of each line, the cleanroom underwent requalification to maintain continuous ISO compliance, especially considering the alterations brought by the new equipment. This requalification process was diligently repeated for all eight lines, thereby upholding stringent quality standards throughout the transfer.
A significant challenge encountered was the documentation gap from the original site. Although PV had access to existing qualification records, these documents did not fully capture the system’s full capabilities. To address this, PV’s Subject Matter Experts (SMEs) undertook a critical initiative to enhance and update these documents. Their efforts brought the documentation in line with the client’s quality benchmarks at the new site, ensuring regulatory compliance and improving operational efficacy. This proactive step set a new precedent in operational excellence and quality assurance for line transfers.
Cementing Trust through Demonstrated Expertise and Operational Efficiency
Throughout the project, there were several key factors that were instrumental in forging a strong trust bond with the client. These included the extensive experience of the Performance Validation (PV) team, their adeptness in identifying and addressing validation gaps, the consistently superior quality of their deliverables, and their autonomy which reinforced the client’s confidence.
Expertise and Proficiency at the Forefront
The seasoned experience of the PV team was central to the project’s success. Their in-depth knowledge of validation processes and mastery of the Valgenesis® Validation Software proved invaluable. This expertise facilitated a smooth and efficient validation approach, vital for a project of this scale and urgency.
Upholding Quality and Validation Standards
PV’s commitment to exceptional quality set them apart. The team’s focus on rigorous process improvement during the validation phase significantly elevated operational capabilities. The objective was not just to meet but to surpass established standards, ensuring every phase of the validation process contributed to a more robust and dependable system.
Autonomy Enhancing Trust
The autonomy exhibited by PV played a crucial role in building client trust. PV’s capacity to independently navigate and make strategic decisions, while staying aligned with project objectives, was highly valued by the client. This autonomy led to more effective and efficient project outcomes, free from external influences.
Achieving Cost Efficiency and Enhanced Performance
A remarkable achievement of the project was the substantial cost savings realized, which notably exceeded the performance metrics of the previous site. The project’s investment was recouped within a mere two months, underscoring the efficiency and efficacy of the strategies implemented.
Rapid and Successful Project Completion
The project was marked by an extraordinary pace: validation of eight lines within a two-year period. This swift timeline was enabled by the client’s engagement and the streamlined processes introduced by PV. The team’s unwavering commitment to excellence, combined with their technical acumen and operational efficiency, played a pivotal role in accelerating the project, all while upholding the highest quality standards.
A Partnership Defined by Trust and Excellence
Through their profound experience, exceptional quality of work, and efficient process management, PV not only achieved the ambitious goals set for the project but also established a profound trust with the client. This project stands as a testament to PV’s capabilities in managing and executing high-stake projects in the medical device sector, marked by precision, efficiency, and a client-centric approach.