AT A GLANCE
A pharmaceutical manufacturer in Illinois requested Performance Validation’s expertise to carry out a two-stage upgrade for their existing process responsible for sterilizing, filling, freeze-drying, offloading, and capping vials. The first stage of the project focused on two large lyophilizers and were executed while production was ongoing, while the second stage focused on the transfer cart and was executed during a temporary shutdown.
In this project, our team focused on the upgrades to the Lyophilizer Cart, which facilitates the transfer of vials from the freeze-drying stage to the accumulation table, where they are later capped. Additionally, PV addressed the control system responsible for overseeing this entire operation. Prior to the upgrade, the system suffered frequent downtime due to motor failures and slow load times, creating a process bottleneck.
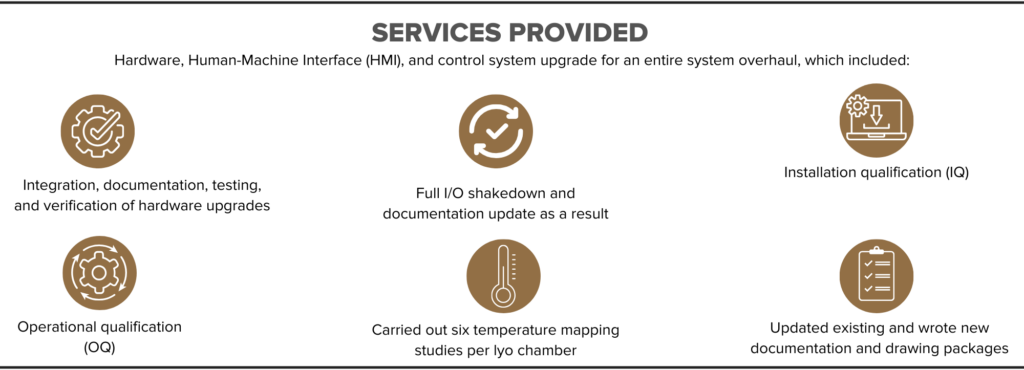
EXPERIENCE WAS CRUCIAL TO A SUCCESSFUL PROJECT
With having a busy team, including new engineers, our client knew they required a team of experienced engineers, especially with temperature mapping, to carry out their project needs. The temperature mapping aspect of the project was critical for ensuring accurate and reliable temperature control during the sterilization and freeze-drying processes. The client recognized that the project required a higher level of knowledge and experience to effectively address this aspect.
During one of the six temperature mapping studies conducted, an unexpected failure occurred with the SIM module on the client’s main temperature mapping equipment. This failure posed a challenge as it required manual intervention from our team to prevent the system from timing out. To continue the study, we had to utilize the client’s older temperature mapping equipment, which fortunately our PV team was trained and experienced with. This proved to be crucial for the project’s success, as the unavailability of trained personnel could have severely disrupted the project for a minimum of five days, until replacement equipment could be obtained. Our familiarity with the older equipment and ability to work with multiple systems ensured that the project stayed on track and avoided significant delays.
HARDWARE AND CONTROL SYSTEM UPGRADE TO ALLEVIATE MOTOR FAILURES
The Lyophilizer’s gaskets and piping were experiencing significant thermal stress due to the steam sterilization and freeze-drying cycles, resulting in frequent failures and decreased reliability. To mitigate these issues, the client conducted a hardware upgrade during the first phase of the project. This upgrade included the implementation of improved materials and designs capable of withstanding the demanding thermal conditions. The objective was to enhance the longevity and reliability of the system, minimizing downtime and improving overall performance. Through the execution of the project documents, PV ensured the upgrades were made correctly and timely. Issues identified by the PV team during the installation verification process were escalated appropriately and addressed before moving on to the next task.
In phase two, the control system needed to be updated to ensure compatibility with the newly upgraded lyophilizer hardware. The outdated control system posed challenges in synchronizing and integrating with the upgraded hardware, hindering seamless operation. To address this, the PV team worked with the client to conduct a comprehensive assessment of the control system and identified the necessary updates and improvements. The goal was to bring the control system up to date, establishing a harmonious relationship between the hardware and software components. This upgrade enabled efficient operation and real-time monitoring of the Lyophilizer Cart.
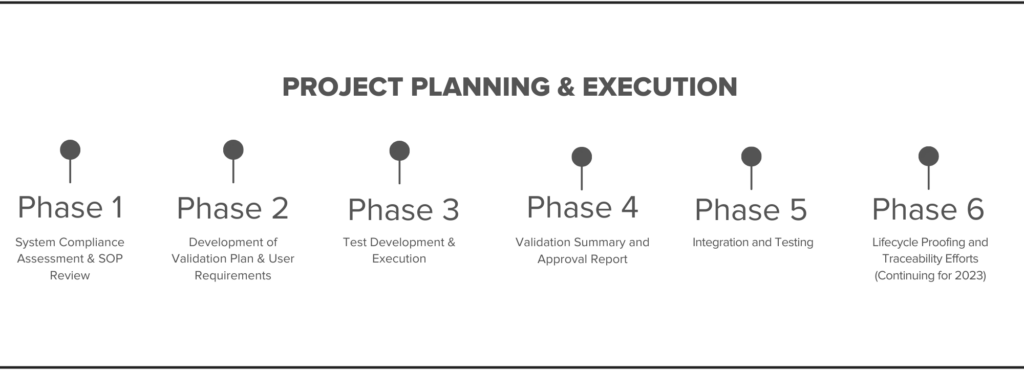
WE WORKED CLOSELY WITH PRODUCTION TO DELIVER THE BEST RESULTS
Our team worked closely with production supervisors, operators, and maintenance workers to get a full picture of what was needed. Our extra effort resulted in a HMI that solved operational problems that were never addressed by their in-house teams in the past.
Our alignment also minimized our impact on production, since the first phase of our upgrade did not involve a shutdown — we personally scheduled tasks to avoid machines that production needed to use and opted to use spare machines to run testing whenever possible. This allowed us to close the project sooner and allowed production to run without any stoppage.
STREAMLINING A PROJECT WITHOUT SACRIFICING QUALITY
During the integration step, we realized that we could halve our execution time by running I/O shakedown and HMI validation at the same time. This allowed us to check alarms, calibrate them, ensure the right graphics were shown on the HMI, and check the position and function of every input and output at the same time. By doing this during production times, the PV team had limited time with the onsite staff. We had to use their time efficiently, and running the shakedown and validation simultaneously was a top contributing factor to the overall success of the project.
UPDATING DOCUMENTATION TO MAKE THEIR NEXT PROJECT EASIER
The operational status of the system was achieved by running the I/O shakedown and validation simultaneously. However, the documentation pertaining to the system was not accurately recorded. To address this issue, PV rewrote the documentation to reflect the actual field-installed equipment. The updated documentation is crucial for expediting future work, as it will prevent any conflicts arising from incorrect drawings or claims that a specific channel is available when it is already occupied by an existing part. By ensuring accurate and up-to-date documentation, future projects will be able to proceed smoothly without any confusion or delays caused by inaccurate information.
Client Testimonial
“I managed a complex controls upgrade for two lyophilizers for which I contracted Performance Validation to prepare and execute the system qualification. This included a controller upgrade, control valve replacement, a SCADA software upgrade, networking of the equipment, and more. Our Validation Engineer provided directions as to general scope and specific details of tests. Execution was limited to a narrow window of time due to implementation falling during a plant shutdown. We received 24/7 support during execution, creative problem-solving when deficiencies occurred, and all aspects of the process were owned by Performance Validation through post-approval. Our upgrades would not have been completed on time and within budget without Performance Validation.”
Lukas R, Project/Automation Engineer
WE TURN CRITICAL INTO COMPLIANT
Our experts at Performance Validation have been commissioning, installing, validating, and qualifying federally regulated industries since 1988. We focus on quality, dedication, teamwork, and delivering projects on time. Our goal is to give you peace of mind during every project.