At A Glance:
A well-established pharmaceutical manufacturer in Kalamazoo, Michigan, embarked on a critical initiative to upgrade their production capabilities, focusing on the implementation of a dual-component vial system. Recognizing the complexity and importance of this project, the manufacturer entrusted Performance Validation (PV) as their validation partner. PV’s expertise was vital in addressing the evolving nature of the project and the increasing production demands, ensuring the development and implementation of the dual-component vial system was executed with precision and efficiency.
Collaborative Effort in Project Management:
Upon joining the project, Performance Validation (PV) was presented with a production line that, while operational, was ready for enhancement to meet growing production demands. The manufacturer required a customized facility, specifically designed to elevate their production capabilities. This upgrade included the integration of lower and upper fillers for the advanced two-chamber vials and modern freeze dryers for improved processing efficiency.
PV stepped in to complement and augment the existing efforts. Their role was to merge their knowledge and resources with the current setup, focusing on upgrading the production line for enhanced efficiency and capacity. This strategic initiative highlighted PV’s commitment to delivering tailored solutions that aligned with the manufacturer’s specific needs and long-term operational objectives.
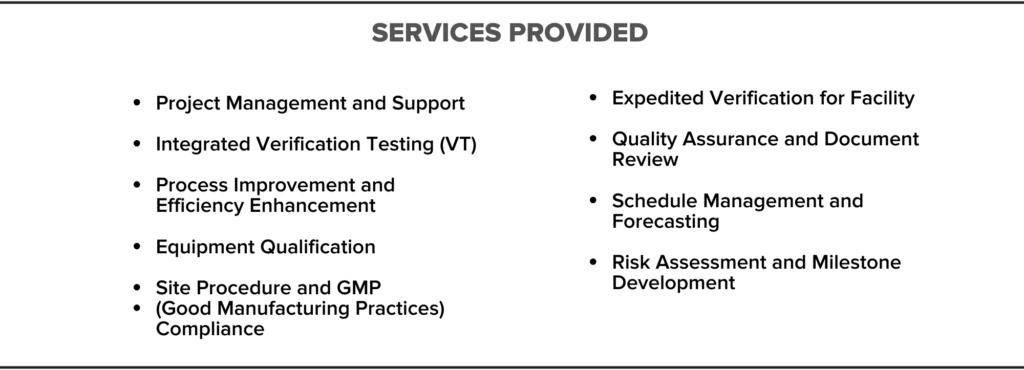
Adapting to New Challenges:
The unexpected onset of the COVID-19 pandemic required a swift and strategic response. The manufacturer, in a proactive move, adapted their production line to accommodate the urgent need for COVID vaccine production. This included repurposing equipment and modifying processes. During this process is when the full PV team took over the project which included switching the line over to producing single-chambered COVID vaccine vials.
Integrated Verification Testing and Equipment Qualification:
Upon taking a more central role in the project, PV conducted a thorough Integrated Verification Testing (VT) phase. This critical step ensured that each component of the production line functioned in unison, from washing and depyrogenation to filling, capping, and tray loading. PV’s meticulous testing protocols were pivotal in confirming the efficiency and reliability of the production line, including the system’s ability to detect and reject defective vials.
Qualification of Vaccine Storage Tanks: Ensuring Precision and Compliance
A pivotal element of this project phase was the qualification of two 800-liter storage tanks, which are integral to the vaccine preservation process. These tanks are not just storage units but critical components in maintaining the vaccine’s efficacy and stability. The qualification process began with a detailed examination and validation of the tanks’ temperature control systems, ensuring they met strict standards for safe and effective vaccine storage. This step was crucial in confirming that the tanks could reliably maintain the precise temperature conditions necessary for vaccine preservation.
In addition to temperature regulation, the tanks’ qualification process encompassed a thorough cleaning protocol. While the initial Factory Acceptance Testing (FAT) provided by the tank manufacturer offered some insights, it produced inconclusive results in certain areas, such as the spray ball testing. Addressing these uncertainties, the client’s quality and operations team requested a retest. This was to ensure the availability of accurate documentation and to confirm that the tank’s specific cleaning equipment was functioning as intended.
Responding to this need, the Performance Validation (PV) team conducted a simulated Clean-in-Place (CIP) cycle. This simulation was more than a mere procedural step; it was a demonstration of PV’s commitment to thoroughness and precision. By successfully completing this CIP cycle, PV provided the client with reassurance and comprehensive documentation. This confirmed that the tanks could be effectively and consistently cleaned to meet industry benchmarks and adhere to stringent Food and Drug Administration (FDA) regulations.
Through these rigorous testing and validation efforts, PV ensured that every aspect of the vaccine storage tanks’ functionality aligned with the highest standards of quality and safety, reflecting their dedication to excellence in every project detail.
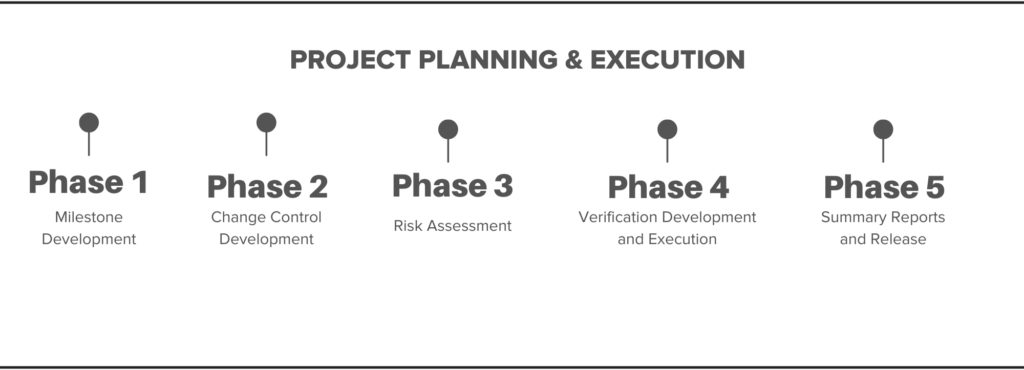
Summary:
In the validation of a dual-component vial production line for a pharmaceutical manufacturer in Kalamazoo, Michigan, Performance Validation demonstrated exceptional adaptability and expertise. They effectively contributed to the project’s transition during the COVID-19 pandemic, managing the conversion for COVID vial production and conducting critical verification testing and equipment qualification. PV’s ability to integrate seamlessly into the project, ensuring adherence to high-quality standards and regulatory compliance, has been paramount in maintaining the project’s momentum and bolstering client trust.